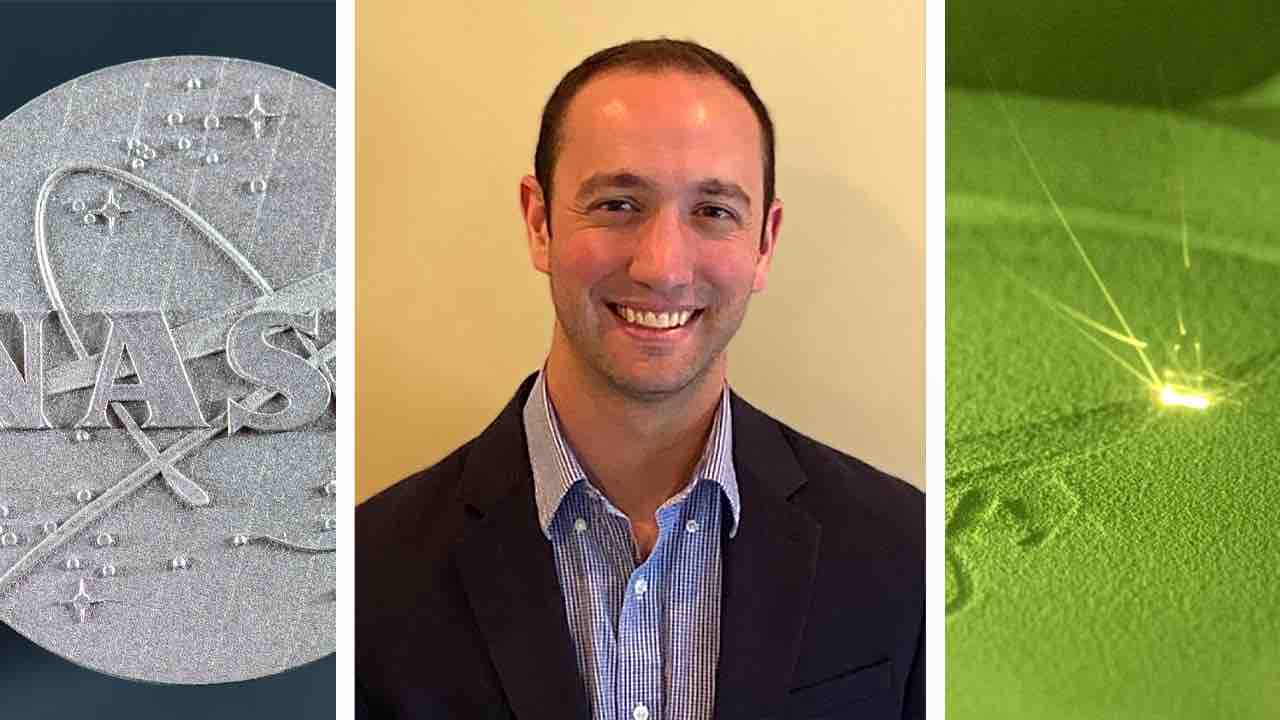
Tim Smith - kosmomagazine.it
We metTim Smith, Research Materials Engineer and Doctor of Philosophy atNASA Glenn Research Center in Cleveland (Ohio, USA). Smith and his team obtained a 3D-Printed superalloy able to withstand more than 1093° Celsius and, above all, is 1.000 times more durable, twice as strong and twice as resistant to oxidation than existing state-of-the-art alloys.
The team, to create the new alloy calledGRX-810, used a laser 3D printing process that fused metals together, layer-by-layer. The goal of this superalloy is to make airplanes and spacecraft much stronger and more durable. To read the official publication of the result obtained, published on Nature, click HERE.
How could the design and construction of aircraft and rockets change if NASA’s new 3D printed superalloy were used? Could this new material be used to re-enter Earth’s atmosphere from space?
Right now, our hope is to either increase the life, increase the operating temperature, or decrease the weight of future aerospace components used in high temperature environments. Maybe we could achieve all three at the same time using this alloy. I’m excited about the possibilities 3D printing this alloy may help realize. Personally, I think the alloy could be used to make heat shields to re-enter the earth’s atmosphere (or help reinforce heat shields), but I should discuss that specific application with the engineers who work that problem before I say that with confidence.
Why is the secret of its resistance the 3D laser printing process and Oxide Dispersion Strengthened (ODS)? How does this super alloy get so strong?
The secret is a combination of the base alloy composition and the nano-sclae oxides we were able to disperse throughout it during the 3D printing process. We had produced ODS alloys before GRX-810 using this new technique but were still unable to get close to the properties that GRX-810 provides.
Credits: NASA/ Jordan Salkin
READ ALSO –> Sarah D’Souza, NASA Ames engineer, talks about Orion Thermal Protection System (TPS)
What are the most important differences between the previous superalloys and the new GRX-810 superalloy?
This alloy was specifically designed for 3D printing. In fact, I doubt you’d be able to replicate its properties by producing it through more conventional methods. We have spent the last two decades trying to 3D print pervious superalloys even though they may not be optimal for that manufacturing process. I think this is an early example of what can be achieved if we start looking at 3D printing as a completely new manufacturing technique that we can leverage to produce materials not possible in the past. In addition, GRX-810 is incredibly stable up to 1093°C compared to many of the past superalloys. This means that you can cycle the alloy to 1093°C back to room temperature many times without its properties degrading. This is not the case for many superalloys.
Your work is very interesting, especially because you manage to create special materials with modern technology and with the right ingredients, such as Y2O3 or Re and B. How do you choose the perfect ingredients to create a superalloy?
We used thermodynamic modelling to help guide which elements to use to produce GRX-810. My colleague, Christopher Kantzos, and I came up with a superalloy microstructure that we thought would compliment the oxide strengthening technique and provide us with the best properties. We then had the thermodynamic models predict the specific composition that would achieve that microstructure and the models appear to have succeeded on the first attempt. I really feel the combination of model-driven design and 3D printing will produce many more exciting materials in the near future.